Fabricante brasileira de embalagens inova processos em apoio à NDC Brasileira, a nova meta climática do Brasil para 2035
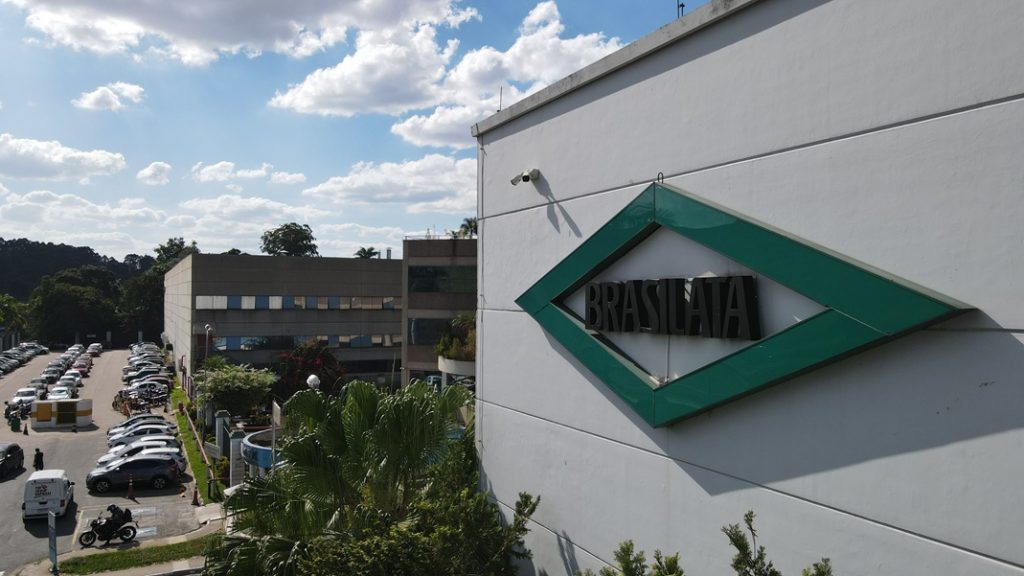
A Brasilata, uma das maiores fabricantes brasileiras de embalagens, se destaca quando se trata de inovar em processos mais sustentáveis. Por meio de um entendimento profundo das necessidades de seus clientes e do comprometimento com a redução de impactos ambientais, a companhia fornece soluções inovadoras e sustentáveis de embalagens para diversas aplicações, como tintas, químicos e indústria alimentícia.
“Toda embalagem gera algum dano ambiental, seja pelos insumos que consome para sua produção ou pelo material de que é composto, que, por vezes, tem um ciclo complexo ou até inexistente de reciclagem, após cessado seu prazo de vida útil”, afirma Tiago Forte, CEO da Brasilata. “O que podemos fazer é pesquisar e desenvolver embalagens que geram menor impacto ambiental ou que possam ter um ciclo de vida prolongado, por ser reciclada ou reutilizada em outros processos fabris”, completa o executivo.
Um dos principais insumos da Brasilata é o aço, que é considerado 100% reciclável. O material consumido pela Brasilata para a confecção de embalagens recebe até 15% de aço reciclado, por conta das características da folha de flandres. “Atualmente temos um plano de gerenciamento de resíduos com esforços direcionados à reciclagem que atende as legislações ambientais vigentes. Além disso, somos associados ao programa da Abeaço, chamado Prolata, que provê pontos de devolução voluntária espalhados em todo o Brasil, proporcionando a logística reversa das embalagens de todas as empresas do setor de embalagens metálicas”, explica Forte.
A segunda matéria-prima utilizada para as embalagens é o plástico. Nessa frente, a Brasilata criou uma solução que utiliza 100% de plástico pós-consumo. O HiBra é um projeto que desde a sua criação trás o DNA sustentável, por se tratar de uma embalagem feita com resina PP-PCR, ou “Polipropileno Pós-Consumo”, uma matéria-prima de fonte reciclada, que evita a produção de plástico virgem, reaproveitando plástico usado e descartado. “É uma solução feita para a categoria de tintas à base de água. A inovação destaca-se por seu alinhamento com as metas e compromissos sustentáveis da cadeia produtiva, ao utilizar materiais 100% recicláveis e pós-consumo”, afirma CEO da empresa.
Ele reforça que, além de embalagens, a Brasilata regula impacto dos insumos de produção, ergonomia, saúde e segurança no ambiente de trabalho. “Recentemente desenvolvemos, em conjunto com a Metal Printing, um solvente para limpeza de máquinas (setup da litografia), que é sensivelmente menos inflamável, com menos odor, e biodegradável, sem risco para o meio ambiente quando em transporte terrestre, hidroviário ou mesmo aéreo”, diz.
Uma outra frente é a Brasilata Labs, que tem como missão desenvolver e comercializar novas tecnologias de impressão em embalagens metálicas. “Aqui nós destacamos o Direct to Metal (D2M), criado em parceria com a Plasmatreat e Actega), que aplica revestimentos UV diretamente no metal, eliminando o uso de estufas movidas a combustíveis fósseis no processo e reduzindo a emissão de poluentes”, explica Gabriel Zaragueta, CEO da Brasilata Labs. “Outra inovação é o Innocan, desenvolvido com a Actega e a HP Indigo, que utiliza impressão digital de alta qualidade em substratos poliméricos que posteriormente são aplicados em chapas metálicas”, diz.
Segundo ele, além da personalização em massa e da qualidade equiparável à offset, o processo reduz emissões de CO₂ em até 40% e é competitivo para pequenos e médios lotes, atendendo padrões rigorosos de segurança. “Ainda estamos em fase de mensuração, mas durante o desenvolvimento desse projeto, já foi perceptível que ele irá gerar menor pegada de carbono se comparado ao processo de produção de embalagens por litografia, ou processo convencional, que conta com estufas térmicas e processos de setup rotineiros”, complementa.
Em 2024, a Brasilata contratou a consultoria da TOTVS ESG Consulting e está em fase final de consolidação dos dados mensurados, onde a partir deles será criado um Plano de Ação para mitigação dos Gases de Efeito Estufa para os próximos anos. Além de corrigir gaps de processos com o intuito de reduzir ainda mais a emissão de poluentes atmosféricos ao meio ambiente, o intuito desse time é pensar em novas formas de produção com menor impacto, apoiando a NDC Brasileira a atingir suas metas. “E isso se dará com a substituição de insumos, melhoria na coleta de dados (qualidade, confiança e celeridade para mensuração), definição de KPIs, treinamentos de temas específicos, entre outras atividades que precisam ocorrer em todas as plantas para que tenhamos uniformidade nos processos e menor impacto socioambiental”, conclui Tiago Forte.